Technology
Tank Head Press Technology
The ALLSTEEL Tank Head Press provides the capability to produce 3 specific types of heads:
The ALLSTEEL Tank Head Press is capable of forming tank heads up to 16’ ( approx 4,900 mm ) diameter, in 3/8” ( approx 9.5 mm ) thick stainless steel, with a dish depth of 24” ( approx 600 mm ).
The press uses servo hydraulics with double ended cylinders to form the knuckle radius and to clamp the part while high-pressure air forms the dish. Rapid approach and return speeds are utilized to minimize the total forming time required.
Standard PLC control system allows easy operator interface; simply enter the part number of the dish to be formed, and all parameters are activated automatically. Therefore: tonnage, knuckle depth, air pressure and flow, and press open height are part of the program data. No data entry is needed once a part is defined.
The PLC supports manual and automatic operation, self-test and data logging as well as remote diagnostics for maintenance purposes. Safety features include over-pressure protection, over-dish protection, provision for light curtain safety barriers, and fail-safe decompression in case of electrical power failure during a dishing operation.
PLC & Hydraulics
The Tank Head Press uses servo hydraulics with double ended cylinders to form the knuckle radius and to clamp the part while high pressure air forms the dish. Rapid approach and return speeds are utilized to minimize the total forming time required.
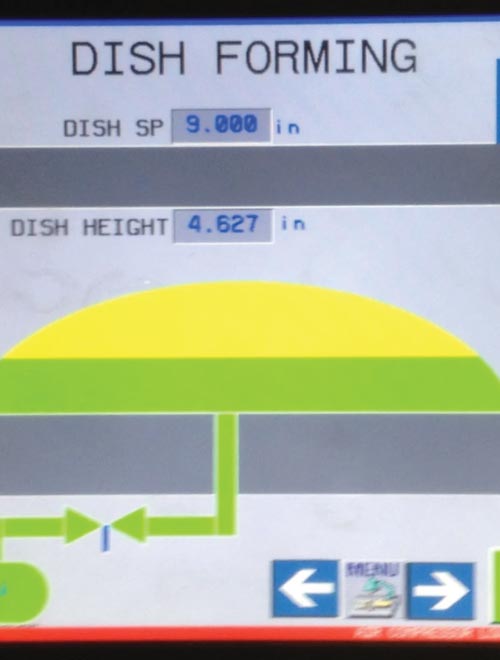