KEY FEATURES OF OUR PRODUCTION PROCESS
FEATURES
VARIOUS TANK HEADS
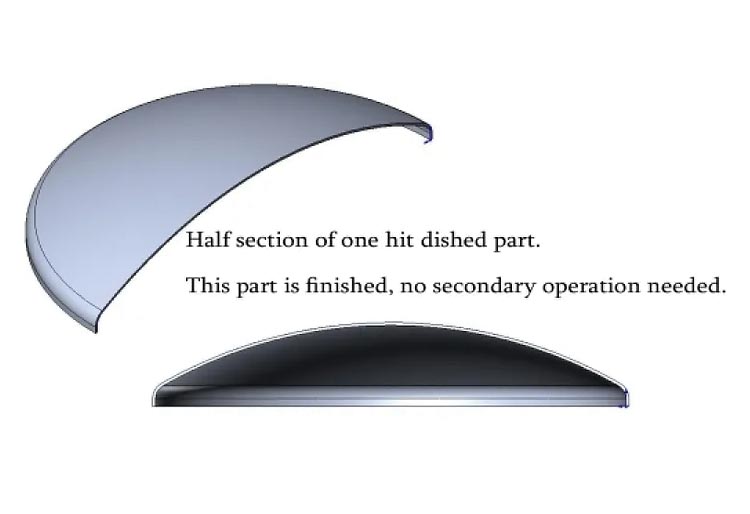
One Hit Precison Blank Tank Head
Guaranteed Excellence
Capital Cost: Highest
Tooling: Hardened Inserts For Top & Bottom Dies
Tonnage: Highest
Productivity: Highest
Secondary Operations: None Required
Flexibility: One Die One Part
Best Application: High Volume, Polished & Precision Parts
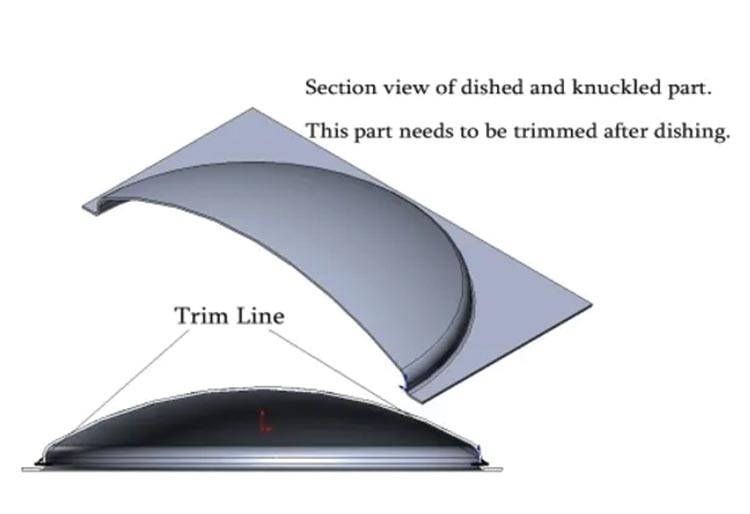
One-Hit Oversize Tank Head
Only the best
Capital Cost: Medium
Tooling: Less Expensive Top & Bottom Dies
Tonnage: Medium
Productivity: Moderate
Secondary Operations: One Trim After Forming Using Multi Axis Plasma
Flexibility: One Die One Part
Best Application: Medium Volume Parts & Thinner Gages
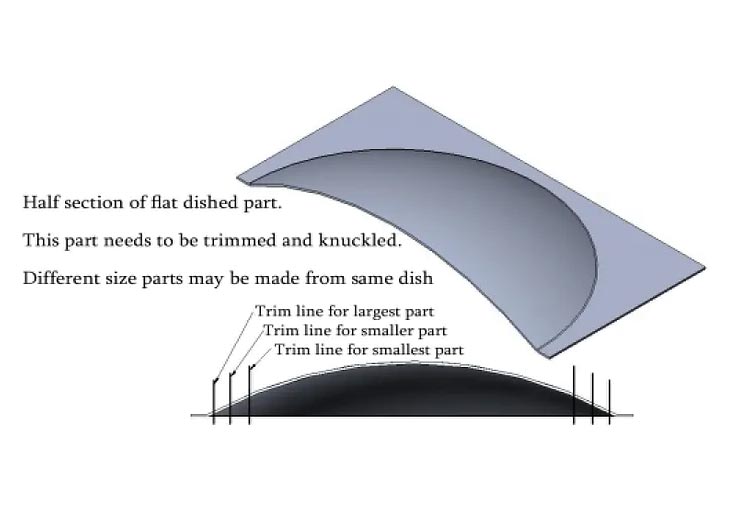
Dishing-Only Oversize Tank Head
To satisfy your needs
Capital Cost: Lowest
Tooling: Lowest Cost (Top Die Only/No Bottom Die)
Tonnage: Lowest
Productivity: Lowest
Secondary Operations: Two Trims, Knuckle & Polish After Forming
Flexibility: One Die For Different Parts/Knuckle Flanged Separately
Best Application: Low Volume Parts, Custom Shapes, Thickest Gages
PROCESS
- This process only requires a female die to form the dish.
- The head material may be pre-polished, and paper protected before air-dishing and the dished area of the head does not need to be re-polished.
- Air-dished heads do not have internal stresses like spun heads.
- These heads do not have distortion problems when holes are cut in them.
- Many different sizes of heads can be made from the same female die.
- The dished head is trimmed to the required size needed to form the knuckle and straight flange. (using a flanging machine)
- Bumped heads are formed using male and female radius dies.
- This process forms a small dished area into the head at a time.
- Many passes are required over the entire area until a dish is formed to the specified radius.
- This process is generally used to form thicker heads.
- This process is not recommended to form thin materials because the dies leave forming marks (“fish scales”) in the head material.
- After the dishing process the heads must be flanged (using a flanging machine).
- Dishing and forming together (ie, flanging the ‘skirt’, also known as knuckling) can be performed in sequence on one ALLSTEEL machine using special tooling, thereby reducing secondary operations.
- The more capital-intensive option, ‘one-hit’ processes allow for higher possible ROIs in the long-run.
- Full ‘one-hit’, or ‘partial-knuckling’ options available depending on materials.
The ‘One-Hit’ process is as follows;
- Flat disk (blank) is placed on top of bottom die.
- Upper die is moved down by press until it contacts blank.
- Press forms the knuckle radius and the skirt .
- Press forces top die to clamp material so it cannot slip while being dished.
- Air under pressure is admitted under the now knuckled part, causing dish to form. Dish depth is monitored by laser sensor.
- Once desired depth is reached, air pressure is released (Dumped into muffler bank) and then hydraulic pressure is also released (Decompression).
- Upper die raised by press, finished part kicked out of upper die by means of air pads .